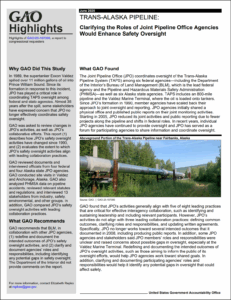
A new report from the Government Accountability Office, or GAO, examines the current status of the Joint Pipeline Office, or JPO.
The JPO is a group of six federal and six state agencies that oversee various parts of the Trans Alaska Pipeline System. The office was formed after the Exxon Valdez oil spill by the Bureau of Land Management and the Alaska Department of Natural Resources to coordinate oversight between the 12 agencies. The last time the GAO reviewed the JPO was in 1995.
In 2023, Senators Lisa Murkowski and Dan Sullivan asked the GAO to conduct the assessment. They specifically asked the GAO to examine the current structure of the organization; how the organization has changed over time; whether the group effectively collaborates to ensure the safety of the pipeline and terminal; and whether the organization has sufficient personnel, resources, and authority to complete its mission.
The Senators’ request came about after a Council-sponsored report found that, among other issues, there had been a reduction in oversight of the terminal in recent years.
“We’ve just begun reviewing the GAO’s report and its recommendations,” says Donna Schantz, executive director for the Council. “We are extremely appreciative of the efforts of Senators Murkowski and Sullivan for requesting this report.”
The JPO: Then and now
“Since its formation in 1990 in response to the Exxon Valdez oil spill, JPO has played a critical role in overseeing the 800-mile pipeline and marine terminal that comprise the Trans-Alaska Pipeline System,” the GAO’s report says.
Until 2004, the JPO’s oversight activities “focused on producing Comprehensive Monitoring Program Reports, reviewing pipeline projects, preventing and responding to oil spills, preparing for the renewal of the TAPS right-of-way agreement, and responding to Alyeska employee concerns,” according to the GAO’s report. The group previously shared an office and published reports on its activities, which it no longer does.
The report says that, according to stakeholders, JPO “scaled back” its work due to a decrease in TAPS projects that required oversight. The report also notes that JPO’s oversight of TAPS was also impacted by shifts in agency roles.
JPO’s current role is unclear
The GAO report notes that the JPO currently functions “as a forum through which participating agencies share information and coordinate activities.”
The GAO recommends the JPO would benefit from outlining the intended outcomes of its current activities “including those aiming to inform the public of its oversight efforts.” This would “enable JPO agencies to work toward shared goals and ensure accountability.”
“Clarifying roles and responsibilities would enhance coordination among JPO agencies and help JPO identify any potential gaps in oversight,” according to the GAO.
The need to identify gaps in regulatory oversight was a significant finding in the Council’s 2023 report (see also “Two years later: Has safety at the terminal improved?”).
“We are encouraged to see the GAO recommend that the JPO needs to clarify its roles and responsibilities,” Schantz said. “The Council had also hoped that the GAO would identify potential gaps in regulatory oversight. Instead, while mentioning that potential gaps are a concern, they have recommended the JPO do this review for gaps themselves.”
In its 1995 review, the GAO noted that the JPO’s success depends on having adequate staffing and funds over the long term. Government agencies have been experiencing reductions in staffing, budgets, and resources for years, with losses increasing at some federal agencies in recent months. The Council is concerned about the JPO’s current capacity to monitor the complex systems at the terminal, along with their ability to follow through on the GAO’s recommendations.
“Everyone involved wants to make sure that oil is transported safely in Alaska,” Schantz said. “Comprehensive regulatory oversight is of critical importance to help ensure that adequate safety systems are in place to prevent devastating events from occurring. This also supports industry and their desire to increase energy development by providing consistency and timely guidance.